The Sustainable Rise of Single-Web Heat-Seal Polyester Films
This article hopes to explain why the growth in single web heat sealable polyester films provides many benefits whilst helping the packaging industry deliver on packaging waste and recycling targets.
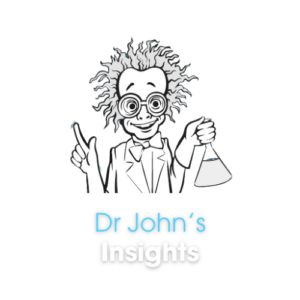
Background
Polyester (PET) is highly recyclable, promoting a sustainable circular economy. It can be made from both virgin and up to 90% post-consumer waste (PCW) resin. However, when PET is combined with other materials in laminated structures, recycling becomes challenging. Chemical recycling is on the rise to separate mixed plastics and reduce landfill waste.
Polyester Films
Oriented polyethylene terephthalate (OPET), or Polyester, was originally not designed as a single-ply, heat-sealable flexible packaging film. It required lamination with materials like polyethylene (PE) or polypropylene (PP) to create the necessary sealant layer.
Polyester offers heat resistance, strength, and a barrier, while the laminated film adds various performance features during packaging. For instance, PE and PP films enhance moisture resistance, seal integrity for gas flushing, and features like anti-fog or peel functionality. PET film is inherently wettable, with wetting angles around 37/38 or 40/42 dynes, depending on the starting monomer. Surface treatment increases film surface energy, improving ink, coating, and adhesive adhesion.
Corona Treatment
Corona treated PET introduced in the 1990’s combined with the appropriate starting monomer can provide an higher wetting level of 50/52 dynes on the corona treated side and 40/42 dynes on the non-corona treated side. This provides the opportunity of printing with different ink types such as solvent, water and vinyl based inks. Corona treatment is an electrical discharge onto the surface of the film as seen in the picture.
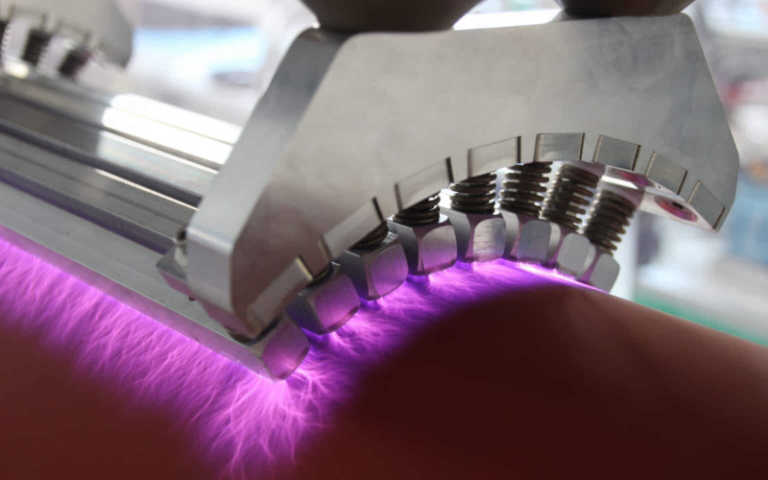
Chemical Treatment
Chemical treatment was favoured for printing in the early days of PET and is effectively a print primer and is normally associated with higher pricing. Development of ink technology obviates the need of chemical treatment but is still preferred in some applications.
Lamination
Lamination of 12um PET films to a sealant layer is appropriate for several reason such as heavy products; durability; different functional performance – barrier, peelability, opacity to light, liquid packaging, bag-in-a-box, reverse printing, extended shelf-life, re-closeability, sterilisable for medical applications and gas flushing.
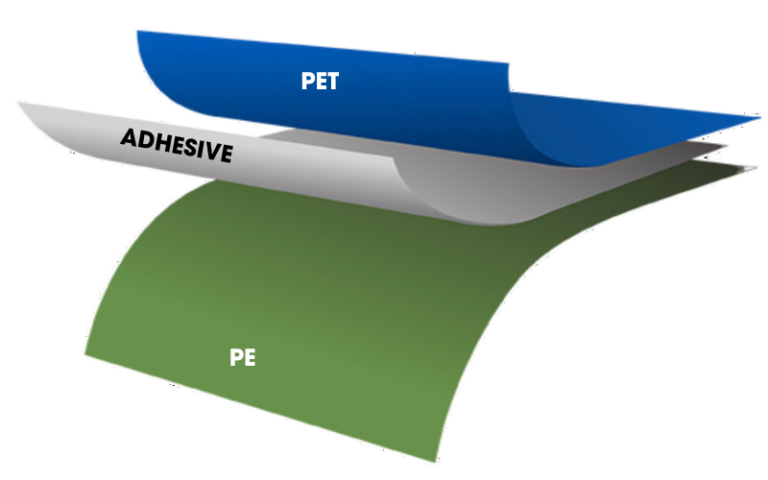
Barrier & thickness
The barrier layer can be altered to suit the application eg. EVOH, AlOx, metallisation. High barrier metallisation can be used to replace aluminium foil for easier recycling. As previously mentioned in the opening paragraph, mixed plastics have to date been more difficult to recycle but with
chemical recycling, this could be overcome.
Thickness of the laminate can range from 35um to say 125um enabling a vast range of products to be packed. Adhesive is used to bond the webs together and can be solvent based, solventless, water based or even extrusion laminated, and can be adjusted accordingly for liquid packaging, sterilisation and retort applications.
Heat-seal PET
Technical developments have provided the ability of extruding
multi-layer films (co-extrusion) enabling a heat seal layer to be extruded within a mono film. and vinyl based inks.
Corona treatment is an electrical discharge onto the surface of the film as seen in the picture.
Heat-seal PET Barriers
PET has a good Moisture and Oxygen Barrier.
The formulation of different multi-layer products can be adapted to suit the appropriate product performance requirements.
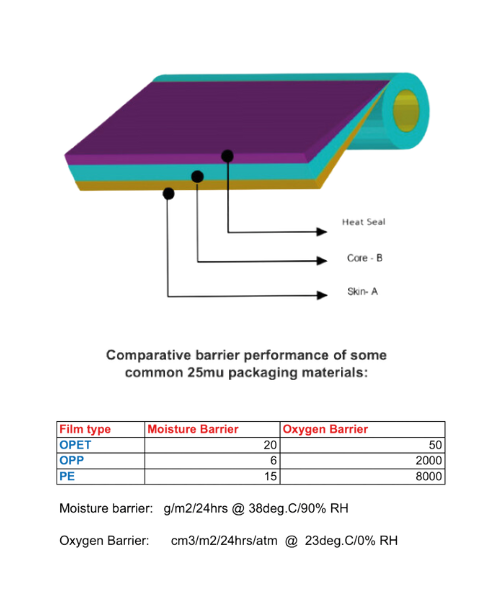
Benefits
A major benefit of heat sealable polyester is that it has high temperature resistance with a sealing range of typically 110-190°C. It can be sealed to
a range of different materials (substrates) such as APET, PETG, CPET, PVC and paper, and benefits by sealing through product contamination.
PET has good oxygen, moisture and aroma barrier to such products as firelighters and perfumed products.
Performance Enhancements
The heat-seal layer can also incorporate technical performance enhancements such as anti-fog and peel functionality. In addition to lower costs and improved recyclability, other benefits of single-ply heat-seal polyester film enables suitability for oven and microwave packaging, sterilisation and deep-freeze.
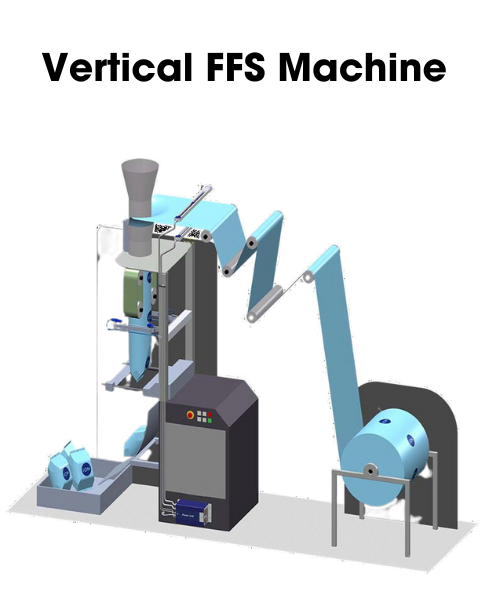
Applications
Packaging applications include overwrapping of products on Vertical and Horizontal form fill-seal machines (VFFS and HFFS) and lidding. Typical products packed include fresh, chilled or frozen food, bakery products, firelighters and perfumed products, confectionery and snacks.
Conclusion
We are excited to offer Heat-seal PET products as part of our portfolio of packaging films.
We hope this article has been informative and we welcome any questions regarding this topic and any enquiries you might have.
Here is a list of the main grades we supply:
PET Heat-seal: Co-extruded
• General purpose heat-seal PET packaging film. One surface of this film is specifically designed for heat sealing (inside) and the other (outside) surface has properties similar to standard PET.
• Material is suitable for sealing to APET, RPET, CPET, PETG, PVC, aluminium foil and paper. The film has excellent transparency, gloss and dimensional stability. The film is used for lidding applications in fresh, chilled or frozen packaging and bakery products. Can be used in pasteurisation, autoclave and sterilisation.
• The film is an excellent base film for metallising and is suitable for high quality printing applications by flexographic or rotogravure. PET film is dual ovenable in temperatures up to typically 200°C.
PET Heat-seal - PCW
The increased recycling of polyester products enables the incorporation of up to 90+ % post consumer waste without detracting from the performance above and is compliant with the UK Government proposed Plastics Tax.
PET Heat-seal - Anti-fog
An anti-fog additive is incorporated into the sealing layer and is designed to heat-seal to APET trays in which the product requires antifogging performance.
PET Heat-seal – Peelable/Anti-fog
This is a transparent three layer film with a peelable and anti-fog functionality on oneside for lidding applications. The film is peelable to PVC, APET, CPET, PETG and to itself. The thicker sealing layer means that it has good sealing properties through product in the seal area. The outer surface is suitable for printing with corona treatment optional.
PET Heat-seal – Peelable
The film is coated on one side with a range of peelable sealing layer providing a strong peelable seal to PVC, APET, CPET, PETG, PS, PE and PP. It provides firm and strong peelable seals but easy opening when required. This film is specially designed for lidding applications either as a single layer or as a two-layer laminate with reverse printed PET or by laminating to paper.